When selecting a Variable Speed Drive (VSD), it is crucial to consider the appropriate sizing of the output choke or sinewave filter. These components play a significant role in managing harmonics and electrical disturbances generated by the VSD during its operation.
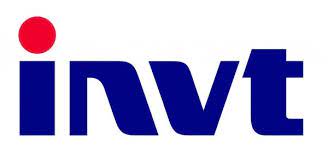
To determine the suitable sizing for the output choke or sinewave filter, the distance between the VSD and the motor needs to be taken into account. Based on the distance, the following guidelines can be followed:
- 0-50 meters: In this range, no choke is typically required. A VSD with the same power rating as the motor (e.g., 30 kW motor with a 30 kW VSD) should be sufficient.
- 50-80 meters: For distances between 50 and 80 meters, an output choke is recommended. The VSD should still have the same power rating as the motor (e.g., 37 kW VSD for a 37 kW motor) but with the addition of an appropriate output choke.
- 80-200 meters: In this range, a sinewave filter becomes necessary. The VSD should have a slightly higher power rating compared to the motor (e.g., a 45 kW VSD for a 30 kW motor) to accommodate the sinewave filter.
It’s important to note that these are general guidelines, and specific manufacturer recommendations and application requirements should always be consulted.
Additionally, when considering VSD selection, it’s essential to pay attention to cable sizing. Calculations should be performed to determine the appropriate cable size, taking into account factors such as voltage drop, current rating, and installation conditions. Proper cable sizing ensures efficient power transmission and prevents issues like excessive voltage drop and overheating.
In summary, when choosing a VSD, carefully consider the distance between the VSD and the motor to determine the need for an output choke or sinewave filter. Additionally, pay close attention to cable sizing calculations to ensure proper power transmission. Consulting manufacturer recommendations and seeking professional assistance can further enhance the selection process.